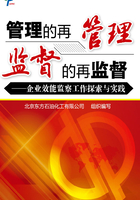
三、组织实施
降低综合损失率是东方石化可持续发展的内在需要。通过开展降低综合损失率工作,找出发生损失的原因,有针对性地加以解决,不但能够提升企业经济效益,而且能实现节能减排、保护环境,提升企业综合竞争实力。
(一)实施精细化的分析,找准问题和差距
精细化管理是在常规管理的基础上进行的,是基于原有管理基础之上的改进、提升和优化。因此,只有分层次、多方位、多角度地分析日常管理中存在的影响损失率的因素,才能找准问题和差距,明确努力方向。
① 东方石化的综合损失率工作基本情况
自东方石化成立以来,在燕山石化的指导下,通过精心组织生产经营,不断加强精细管理,持续深化内部改革,各项工作都取得了显著的成绩。但随着与燕山石化和中石化各项工作的进一步接轨,东方石化各项工作与同行业先进企业的差距进一步显现,其中,最直接反映装置管理水平的综合损失率指标与燕山石化等国内同类装置相比,差距就很大,比如,2009年燕山石化各生产单位的月度综合损失率平均能够控制在0.6%以下,而东方石化各生产单位2009年的月度综合损失率最好只能达到1.6%,最高达到2.9%。
东方石化降低综合损失率工作涉及4个生产单位、6大系列产品共19套生产装置。每个生产企业均涉及原(辅)料损失、装置加工损失和产(成)品损失等三个环节。
东方石化19套装置基本情况如下。
② 东方石化综合损失率工作存在的主要问题及主攻方向
通过对东方石化4个生产单位、19套生产装置、57个重点环节的损失率情况进行综合分析,总体来讲,东方石化主要存在以下三个方面的问题。
一是在原料损失方面,计量误差较大,导致原料损失率上升。以助剂二厂为例,2009年原料损失在综合损失里占了43.5%的比例。
二是在装置加工损失方面:由于装置生产过程中生成的在目前的工艺条件下不具备回收条件的副产物的理论产出量与实际产出量偏差较大,造成加工损失率较高。据统计,2009年东方石化的综合损失率为1.98%,其中生产加工损失率为1.40%,占全部损失量的86.41%。
三是在产成品损失方面:由于工厂综合配套不完善,没有形成资源的综合回收利用,各生产单位均不具备彻底消灭火炬的条件。
针对上述问题,东方石化多次召开专题会议进行研讨,公司领导和相关部室深入基层进行现场办公,深入调查和掌握公司损失率指标的现状和存在的问题,找出四个方面的主攻努力方向。一是确保计量准确。完善计量系统,加强统计分析。进一步提高计量系统的精确度,减少计量误差。制定分段计量分段考核的办法,协调处理好厂际之间的计量纠纷,将损失减到最小。二是优化装置运行。提高操作人员的技术水平,坚决杜绝误操作,最大限度地减少非计划停车次数和时数,保持装置安稳长满优运行。三是推进技术改造。按计划,逐步实施有机化工厂VAC装置尾气乙烯回收、助剂二厂尾气回收利用、化工四厂火炬气回收利用等技术改造项目,降低综合损失率。四是加强日常管理。消除装置跑、冒、滴、漏现象,减少装置生产物料的非计量损耗。加强班组经济核算,将损失率指标进行层层分解,落实到班组,增强职工的责任心。
(二)实施精细化的规划,明确责任和目标
正确地分析形势,科学精确地定位,是实现精细化规划的关键。因此,只有抓住影响降低损失率工作的关键环节和主要矛盾,才能明确责任分工,确定出通过努力可以达到的目标。
① 成立组织机构
成立了由公司总经理、党委书记任组长,领导班子其他成员为副组长,公司各部室负责人和各二级单位党政正职为组员的降低综合损失率管理监督领导小组,负责研究部署、指导和组织检查所属企业的降低综合损失率管理监督工作,协调降低综合损失率管理工作关系,处理与降低综合损失率管理有关的重大事宜。成立了由公司各部室人员组成的工作小组,负责对各单位降低综合损失率管理监督的指导、审查、督办和考核,形成了行政主要领导负责,监察部门组织协调,相关职能部门积极配合,基层单位具体实施,广大职工全员参与的领导体制和运行机制。
② 确定降低损失率工作目标
在认真分析东方石化损失率现状及与先进企业的差距的基础上,东方石化降低综合损失率管理监督领导小组经过研究决定,2010年各生产单位综合损失率目标为降到1%以下,同时本着“持续改进、不断提高”的原则,实行动态管理,随着工作的推进,每个阶段根据指标完成情况,不断提升新的指标,促进了各生产单位不断强化管理、整改落实,使装置损失率、综合损失率等指标逐年、逐月降低。
(三)实施精细化的控制,建立制度和机制
企业要实现精细化,必须实现由随意化管理向规范化、制度化管理的转变;一套好的制度和一整套协调、灵活、高效的运行机制,可以推进企业各项工作更加规范、高效。因此,只有建立和完善有效的制度和机制,才能激励职工参与的积极性和自觉性,确保了降低损失率工作顺利推进。
① 建立专项例会制度
公司每月召开一次降低综合损失率管理监督工作例会,由各生产单位以PPT的形式汇报本单位上个月损失率指标额完成情况,及下一步的工作重点和需要协调解决的问题;例会有公司降低综合损失率领导小组、公司各职能部门负责人、各二级单位的行政正职参加。会议的定期召开及相关领导、专业部门领导的出席,实现了工作沟通在第一时间内完成、信息资源在第一时间内共享、困难问题在第一时间内解决,建立形成了配合默契、高效有序的工作格局。
② 强化宣传发动机制
两年来,东方石化坚持把思想动员作为降低损失率工作的切入点来抓,加大宣传发动力度,提高全公司广大员工对降低损失率工作重要性的认识,在全公司上下形成了齐心协力抓降损、快马加鞭抓进度的浓厚氛围。为扩大工作声势,注重依托东方石化报、各企业简报、信息、网站等平台,对降低损失率工作进行全方位、多形式、大力度的宣传,做到了报纸期期有声音、信息日日有动态,提升了干部职工对降低损失率工作的参与度和关注度,使降低综合损失率工作获得了深厚的群众基础,成为广大干部职工的共识和自觉行动。
③ 形成监督检查机制
为了深入推进降低损失率工作的开展,两年来,东方石化公司把“降低综合损失率”列为公司级重点效能监察项目,实行全程管理监控。按照效能监察的工作程序和要求,两级纪委分别制订实施方案,组织专项会议,及时沟通信息,加强跟踪督导,开展过程监察,有效促进了降低损失率工作的顺利开展。
(四)实施精细化的操作,落实任务和措施
精细管理的本质意义就在于它是一种对战略和目标分解细化和落实的过程,也是提升企业整体执行能力的一个重要途径。因此,只有把降低损失率任务分解细化到公司19套装置及原料、生产和产成品等各个环节,把降低损失率责任落实到每个岗位的每一名职工,才能够提高执行力,通过一个步骤一个步骤地完成,一个目标一个目标地实现,全面实现预期的降低损失率目标。
① 制定“四定”措施
公司经营计划部和党群工作部联合下发《关于进一步细化降低综合损失率具体措施的通知》,各生产单位干部职工积极转变观念、创新思维,打破原有的思想束缚,从原料进厂、检验计量、原料储存、生产加工、产品储存、产品出厂计量等各环节入手,深入分析损失率的实际状况,查找可能存在的损失点,并针对每一可能的损失点定“四定表”,即“定具体措施、定责任人、定完成时间、定目标或预期效果”。“四定”措施不但实现了目标任务的分解细化和落实,更重要的是,它打破了单套装置优化的局限,开创了装置之间、厂际之间优化的先例,实现了生产从原料入厂到产品出厂的全覆盖、全流程管理,做到纵向到底,横向到边,确保守住各生产环节。两年来,共制定降低损失率“四定”措施349条,通过狠抓各项措施的落实,降低损失率工作取得了实实在在的成效。

班组职工正在分析经济核算结果
② 狠抓原料、产品出入厂和储存环节的管理,降低原料损失和产品损失
第一,在提高计量环节准确率方面,对涉及各生产厂物料、能源盘点结算的计量点和仪表自控率情况进行统计核查,全公司共涉及计量仪表281块。通过集中进行仪表校验、加装、改造和补充工作,极大地改善了统计数据的可靠性,为物料损失的准确统计提供可靠依据。东方化工厂针对汽车过衡数据偏差波动较大的问题,专门组织了轨道衡试验,修改了《轨道衡过衡操作法》,实现了轨道衡过衡计量操作准确率99.83%。第二,在狠抓原料入厂、产品出厂各环节管理方面,修订并落实车辆进出厂管理制度,建立产品、原辅料空车质量档案;加强对车辆出厂的监控、不定期进行抽检,堵塞了车辆在计量环节作弊等管理漏洞;严格控制大宗原料石脑油的卸净率,自制了耙子用于人工清理罐底料,有效降低了物料损失;强化装卸台账和原料台账的记录和监控,2010年针对储运二厂铁路醋酸罐车卸车损耗高(最高达到2.06%)、化工一厂乙烯增压系统损耗大(日损耗量3~4吨/天,最大曾达到30吨/天)等问题进行了调研,在上级部门的协调下进行了流程优化,使原料损耗持续保持在0.1%以下。第三,在狠抓仓储环节管理方面,建立了旬盘旬报制度,改以往的月盘点为旬盘点,做到了及时发现存在的问题,及时调查分析并采取应对措施,有效控制了原料、产品的库耗率。东方化工厂加强罐区管理,通过采用储罐罐体喷淋、储罐内部循环水盘管的检查和确认等措施,解决了夏季炎热气候造成的物料损耗增加的问题。化工四厂通过制定“重油选料管理办法”严把重油质量关,将重油的质量突变对装置的影响降到最低,保证装置的稳定运行。
③ 狠抓生产运行环节的管理,降低装置加工损失
实践证明,装置的安稳运行对降低损失率至关重要。东方石化从确保装置的稳定运行入手,采取了一系列的有效措施。第一,加强对操作人员的培训,提升职工的操作水平和应急处理能力。由于操作人员在应对工艺波动、关键设备突发故障等意外事件时处理得当,避免了多起非计划停车以及由此产生的物料损耗。第二,开展平稳度操作竞赛和班组经济核算活动。将装置运行过程中的关键控制指标上墙,激发操作人员精心操作的潜能。通过班组经济核算让一线职工算小账、算细账,有效增强了广大职工节能降耗的意识。第三,不断固化各项优化操作流程和管理流程。两年来,各单位制定了《装置波动期间降低生产损失量工作预案》、《轨道衡过衡操作法》、《重油选料管理办法》等12项制度和规程,保证了降低损失率效果的持续稳定。
④ 狠抓技改技措项目的实施,降低装置加工损失
针对装置本身存在的尾气放空、火炬气等影响损失率的突出问题,两年来,东方石化按计划稳步推进技术改造工作,共实施相关的技术改造项目24项。其中影响装置损失率的尾气回收和利用项目成效最为显著,东方化工厂煤粉炉掺烧项目已于2011年8月顺利投用,初步核算每年可节约原煤采购成本280余万元;有机化工厂VAE尾气回收装置于2010年9月开始稳定运行,实现了每月回收乙烯近百吨;助剂二厂聚乙烯装置尾气回收利用项目于2010年9月投运,达到了预期效果。另外,各单位还认真分析各套装置物料平衡情况,通过实施小型技术改造尽可能回收和循环利用原设计中放空的物料,有效降低了物料的损耗。

检修人员正在消除阀门漏点
⑤ 狠抓日常管理和点滴回收,降低综合损失
第一,加强装置日常管理,做好设备的巡回检查和维护保养,及时发现和消除“跑、冒、滴、漏”,减少装置的泄漏损失。第二,加强分析取样管理。立足点滴回收,最大限度做好分析取样时的物料回收工作,减少不必要的物料损失。第三,加强检维修管理。对检维修过程中排放的物料进行回收再利用,尽可能地减少检修时的物料损失。
(五)实施精细化的核算,严格考核和奖惩
精细化的核算,是企业认识自身经营情况的必要条件。只有通过精细化的核算,建立一套系统的、比较完备的奖惩机制,使干部职工明确具体目标,才能够有效发挥激励作用和制约作用,促进员工积极主动参与到降低损失率工作中来。
① 建立专项考核制度
在公司原有《经济责任制考核细则》基础上,将损失率指标纳入经济责任制考核,增加损失率考核专项部分,并且每半年对各项考核指标进行及时修订,做到奖优罚劣,极大地激发了广大干部职工的工作热情和工作干劲。公司党委把降低综合损失率工作作为对领导干部素质、作风的考验和能力的体现,纳入对领导干部的考核。
② 建立赶先进、促后进的机制
随着降低损失率工作的逐步推进,面对综合损失率明显降低、“降低损失率”工作难度逐步加大的现实,为进一步挖掘装置潜能、发挥职工的潜力,东方石化在全公司范围内组织开展了“生产装置竞赛”活动,建立了赶先进、促后进的机制。各生产厂、各装置积极对标国内同行先进标准,深入查找自身差距和不足,深入剖析原因,及时找准努力方向,狠抓各项降低损失率措施的落实。公司每月通过对19套装置损失率情况、指标创新、指标行业排名等进行排名、奖励,并在报纸上定期公布,激励各生产单位“跳起来摘桃子”。2011年全年,公司对19套装置累计奖励227次,累计奖励金额228.147万元,广大员工立足岗位、精心操作、节能降耗的自觉性显著增强。
两年来,东方石化应用精细化管理模式,从建立健全制度机制入手,调动全公司上下3900余名在岗职工的积极性,为企业降低损失率工作献计献策,形成全员参与、上下联动的运行模式;以细化措施分解责任为突破口,查找19套装置57个重点环节存在的可能损失并采取有针对性的措施,形成围绕装置各环节和生产全过程的运作模式,推动了公司降低综合损失率工作的全面有效实施。