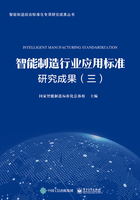
7 数字化管控要求
7.1 数字化生产模型
7.1.1 车间模型
7.1.1.1 总则
图 4 数字化车间模型
7.1.1.2 组织结构管理
根据芯片式传感器企业生产加工特点,以树形图的方式展示车间组织结构关系,主要包括以下属性信息:
—— 车间名称;
—— 车间编码;
—— 所属工厂。
7.1.1.3 物理布局管理
对车间进行物理布局划分,主要包括生产区域和生产位置两个部分。
生产区域包括以下属性信息:
—— 生产区域名称;
—— 生产区域编码;
—— 所属车间。
生产位置包括以下属性信息:
—— 生产位置名称;
—— 生产位置编码;
—— 所属区域。
7.1.1.4 生产单元管理
生产单元通常为实际的生产设备,主要包括以下属性信息:
—— 生产单元名称;
—— 生产单元编码;
—— 生产单元类型;
—— 生产单元描述。
7.1.1.5 能力及能力组管理
能力组及能力用于描述生产单元的生产能力。
生产能力组包括以下属性信息:
—— 能力组名称;
—— 能力组编码;
—— 能力组描述。
生产能力包括以下属性信息:
—— 能力名称;
—— 能力编码;
—— 能力描述。
7.1.1.6 变量及变量组管理
变量组及变量用于描述生产单元的数据采集信息,主要包括基本属性、数据源属性和采集属性。
基本属性包括以下信息:
—— 变量名称;
—— 变量组名称;
—— 计量单位名称;
—— 数据类型;
—— 变量编码;
—— 变量描述。
数据源属性包括以下属性信息:
—— 数据源类型;
—— 数据源名称;
—— 变量标签。
采样属性包括以下属性信息:
—— 采样类型;
—— 采样周期;
—— 采样偏移量;
—— 采样精度;
—— 采样方式;
—— 采样处理逻辑。
7.1.2 产品模型
7.1.2.1 物料类型管理
物料类型主要包括以下属性信息:
—— 物料类型名称;
—— 物料类型编码;
—— 物料类型描述。
7.1.2.2 物料信息管理
物料主要包括以下属性信息:
—— 物料名称;
—— 物料类型;
—— 物料供应商;
—— 物料编码;
—— 物料描述。
7.1.2.3 产品家族管理
产品家族是产品的逻辑分组,一种产品只能隶属于一个产品家族,但一个产品家族可以包含多种产品。产品家族包括以下属性信息:
—— 产品家族名称;
—— 产品家族描述。
7.1.2.4 产品信息管理
产品主要包括以下属性信息:
—— 产品名称;
—— 产品家族;
—— 产品编码;
—— 产品描述。
7.1.2.5 物料清单管理
物料清单(BOM)描述了芯片式传感器产品的组成,一般包括以下属性信息:
—— BOM 名称;
—— 版本号;
—— 产品名称;
—— BOM 编码;
—— BOM 描述。
物料清单项一般包括以下属性信息:
—— 物料名称;
—— 投料量;
—— 计量单位;
—— 投料顺序。
当某一物料存在替代物料时,替代物料一般包括以下属性信息:
—— 物料名称;
—— 替代投料量;
—— 计量单位;
—— 优先级。
7.1.3 工艺模型
7.1.3.1 工艺路线管理
工艺路线由菜单组成,组成芯片式传感器工艺的工艺约束及物料需求在菜单模型中描述。
菜单包括以下属性信息:
—— 菜单名称;
—— 菜单编码;
—— 菜单版本;
—— 关联能力组;
—— 关联能力;
—— 关联物料;
—— 菜单描述。
菜单约束包括以下属性信息:
—— 进站或出站约束;
—— 物料主类型约束;
—— 物料子类型约束。
工艺路线包括以下属性信息:
—— 工艺名称;
—— 工艺编码;
—— 工艺类型(主工艺路线或调用工艺路线);
—— 工艺版本;
—— 工艺路线节点序列。
工艺路线节点中的返工工艺节点包括以下属性信息:
—— 返回主工序时的菜单;
—— 返工次数;
—— 从返工工序出站时返回主工序时的菜单。
7.1.3.2 工艺信息管理
工艺信息管理对菜单进行工艺参数说明,包括以下属性信息:
—— 参数名称;
—— 参数类型;
—— 参数值;
—— 参数值上限;
—— 参数值下限;
—— 参数顺序。
7.1.4 生产事件模型
7.1.4.1 事件类型管理
事件类型包括以下属性信息:
—— 事件类型;
—— 事件类型名称;
—— 事件类型描述。
7.1.4.2 事件模板管理
事件模板用于定义事件模板名称、描述、所属事件类型、是否基于时间,以及模型版本号等基本信息,可以在事件模板中通过绑定标签、存储过程、动态链接库等属性,定义事件的触发条件或者事件触发后的处理逻辑。
7.1.4.3 事件管理
事件是事件模板的实例化,需要定义触发事件的条件和触发后需要处理的逻辑等信息,具体包括以下属性信息:
—— 事件类型;
—— 事件模板;
—— 事件触发条件;
—— 事件执行操作。
7.1.5 生产模型数据结构关系
有关车间模型、产品模型、工艺模型和事件模型中各要素的数据结构关系可分别参见附录 A.1、A.2、A.3 和 A.4。
7.2 车间计划管理
7.2.1 总则
车间计划管理按照业务流程划分为接收层、排产层和调度层三个层次,包含的具体功能、各功能之间及与外部功能子系统之间的数据关系描述如图 5 所示。
图 5 数字化车间计划管理功能模型
7.2.2 接收层功能
a)生产计划接收与维护
接收外部系统下达或导入的生产订单。能够检测订单的关联数据完整性,包括如生产设备信息、工艺流程、生产时间、工作日历等信息。如果信息不完整,需要对相关数据进行补充。
b)产能分析管理
根据生产线生产单元配置信息、设备生产速度设置信息,以及当前生产线生产任务完成情况,得出生产线生产能力。
c)每日(次)排产批次管理
安排每日(次)排产批次订单,并从“产能分析管理”获取生产线能够提供的产能,来控制每次投单的数量,实现需求产能与提供产能的匹配。
7.2.3 排产层功能
a)排产参数设置
设置排产相关参数,如设备负载率、优化目标、优先级、排产约束等。主要的排产约束条件有:
—— 时间窗约束。通过给定每个工序生产时间窗,限定每个工序并行设备的工作时间范围。生产批次受到设备生产时间窗约束。
—— 有限缓冲区约束。构建缓冲区中的等待队列,生产批次出入缓冲区过程中受到工序间缓冲区容量限制,并受工艺条件中要求的器件最长等待时间的约束。
—— 关联工序设备约束。关联工序设备约束的加工阶段要在与上道工序加工设备对应的设备上进行加工约束。
—— 工装产能约束。使用相同模具的生产批次,受到生产线包含模具所能提供的最大产能约束。
—— 产品类型匹配的设备产能约束。投产的生产批次,受到生产线上可以生产同一种类型产品的设备所能提供的最大产能约束。
—— 瓶颈产能约束。滚动排产过程中,单日投产的生产批次的需求产能受到瓶颈工序设备提供的产能的限制。
b)投产批次订单优化
基于生产订单的产品类型、物料需求、改机或更换工装、生产设备、交货期等信息,对计划工单的上线顺序进行优化。
c)详细排产
基于约束条件和配置信息进行详细排产,得到生产排次在每个工序被指定的加工单元、开工时间、完工时间等排产结果。
d)排产结果确认与调整
对于自动排产的结果,可以人工进行修改和调整,确认无误后方可下发到车间现场。
e)生产数据分析
根据批次追踪数据和设备运行状况,分析排产结果执行情况,调整排产参数设置;根据质量检测结果,调整排产参数设置。
7.2.4 调度层功能
a)生产状态反馈
接收和处理生产计划执行过程中的各类反馈信息,主要包括设备运行状态、过程质量情况及工单执行情况。
b)生产现场调度
将详细排产结果导入生产现场调度系统,生产现场调度要依据投产批次生产进度、设备实时运行状况和质量检测数据,调整和分派生产批次,并使得生产线的实际生产情况能够逼近排产计划。
7.3 车间在制品管理
7.3.1 总则
车间在制品管理包含的功能模块主要有生产检查、批次物料分配、生产过程记录、批次状态控制,如图 6 所示。
图 6 数字化车间在制品管理功能模型
7.3.2 生产检查
生产检查主要是核查生产是否符合工艺规范,主要包括:
—— 投产原料检查:检查投产原料类型是否与 BOM 规定的原料类型一致,防止错误投料。
—— 工艺时间检查:监测批次等待生产的时长/加工过程时长,对于超过工艺要求的最大等待时长的批次进行报警,对于未满足工艺要求的最小加工时长的批次禁止报完工。
—— 设备菜单检查:检查工艺要求指定的设备菜单与设备上实际执行的菜单是否一致。
—— 工装检查:检查使用的工装类型是否与工艺要求规定类型一致,检查工装是否达到使用寿命。
7.3.3 批次物料分配
批次物料分配是根据实际生产情况为批次分配对应的生产物料,通过扫描物料条码实现与批次的绑定。批次物料分配的情况包括:
—— 批次开始生产前,根据投产数量和 BOM 规定的原料类型为批次分配原料。
—— 将两个或多个批次的原料合并分配给一个新的批次。
—— 一个父批次分成多个子批次,并将父批次的原料分配给各个子批次。
—— 从一个批次中分割出返工子批次,并将原批次中需要返工的原料分配给返工子批次。
—— 对于未通过测试的原料从批次中剔除。
7.3.4 生产过程记录
生产过程记录是记录在制品的生产过程中涉及的关键数据信息(人、机、料、法、环),记录的时机和关键信息包括:
—— 在批次导入到相应的设备中进行加工时,需要记录批次编号、设备编号、导入时间、操作人编号、使用工艺名称,以及环境温湿度等。
—— 在批次加工完成后从设备中移出时,需要记录批次编号、移出时间、工艺指标的测试数据等。
—— 在批次暂停生产时,需要记录批次编号、暂停原因、操作人编号、暂停时间等。
—— 在批次恢复生产时,需要记录批次编号、恢复原因、操作人编号、恢复时间等。
—— 在批次停止当前生产并退回到等待加工时,需要记录批次编号、退回原因、退回时间、操作人编号等。
—— 在批次终止生产时,需要记录批次编号、终止原因、终止时间、操作人编号等。
7.3.5 批次状态控制
批次状态控制是通过对批次执行操作从而改变处于生产线上的批次状态,引起批次状态改变的操作包括:
—— 批次投料会将批次从就绪状态变更为等待状态。
—— 入机台会将批次从等待状态变更为加工状态。
—— 出机台会将批次从加工状态变更为完工状态(非最后一道工艺)或结束状态(最后一道工艺)。
—— 扣押会将批次变更为暂停状态。
—— 释放会将批次从暂停状态变更为扣押之前的状态。
—— 回退会将批次从加工状态变更为等待状态。
—— 入库会将批次从结束状态变更为库存状态。
—— 终止会将批次变更为结束状态。
7.4 车间质量管理
7.4.1 总则
数字化车间质量管理主要功能包括质量数据采集、质量检测与监控、质量追溯。各功能之间及与外部功能子系统之间的数据关系描述如图 7 所示。
7.4.2 质量数据采集
质量数据采集主要来源于设备和人工两个方面,具体的数据内容如下:
—— 生产设备数据:按照生产工艺,包括诸如光刻机、划片机、涂胶机等设备,采集相应设备的运行工艺参数,如涂胶机的涂胶匀胶转速、划片机的刀片压力和划片深度等。
—— 质检设备数据:对不同生产工序的质检指标进行采集,如镀膜工艺的检测指标包括膜厚度和折射率,光刻工艺的检测指标包括线宽和光刻精度等。同时,包括传感器芯片检测环节的电参数测试、高低温测试、压力测试及失效分析等检测数据。
—— 人工检测数据:主要包括人工目测检测数据,诸如传感器芯片的外观缺陷等。
与质量相关的其他数据还包括片料、元件等物料质检数据,洁净度等级,温度、湿度等生产环境数据。
图 7 数字化车间质量管理功能模型
7.4.3 质量检测与监控
7.4.3.1 质量检测
在芯片式传感器工艺过程中,包含多工序的在线质量检测、半成品及成品的筛选,普遍通过专有质检设备实现自动化检测。数字化车间管控应能够对相应检测指标数据进行准确采集,为在线质量控制和判定分析提供可靠依据。
7.4.3.2 SPC 在线分析
对于能够实时采集的关键质量参数,应采用统计过程控制(SPC)方法实现在线质量分析,以达到及时发现质量缺陷和有效评估过程质量的目的。具体要求能够提供基于控制图的实时监测画面对质量异常情况进行及时报警;能够基于采集数据计算过程能力指数(CPK)等评价指标。
7.4.3.3 APC 实时控制
先进过程控制(APC)方法,主要包括设备故障检测与分类(FDC)技术及批次到批次(R2R)自动反馈控制技术两个方面。采用自动化的方式,能够自动侦测和反馈设备及工艺的波动,并采取自动补偿的方法进行控制调节,从而稳定工艺质量。如在光刻工艺进行运用,可以有效减少试片和返工的次数,提高设备使用效率;当工艺稳定时,可以减少测试晶圆的数量和频次,起到降低成本的效果。
7.4.3.4 不合格品处理
对于判定为不合格的工序半成品或成品,应按照标准的流程进行处理,重点管理返工流程。基于返工产品的质量状态,有效控制返工过程和返工次数。
7.4.4 质量追溯
7.4.4.1 质量追溯标识
在芯片式传感器生产过程中,主要的标识信息包括晶圆编码、晶舟编码、相关物料编码、半成品编码及成品编码等,通过对这些标识的关联识别,为质量追溯提供必要条件。
7.4.4.2 产品质量档案
通过标识可以追溯产品生产过程中与质量相关的关键信息,形成完整的产品质量档案。应包括以下信息内容:
—— 产品信息:品名、规格/型号、产品批号/编码、生产日期、BOM 及工艺标准版本等。
—— 产品质量信息:原辅料、中间产品、成品、包装等质量信息。
—— 过程质量信息:各生产区域及工序的生产过程质量信息,如工艺控制参数、检测指标等。
—— 质量判定信息:各环节质量判定、审核、返工、放行等质量决策的时间、人员等处理过程 信息,以及各类质量事件的处理过程信息。
7.5 车间物流管理
7.5.1 总则
数字化车间物流管理主要功能包括物料存储、物流调度、物流跟踪、消耗成本。各功能之间及与外部功能子系统之间的数据关系描述如图 8 所示。
图 8 数字化车间物流管理功能模型
7.5.2 物料存储
芯片式传感器在芯片生产过程中,各工序应按照 BOM 要求将生产物料存放在生产线旁,并提供存储区域作为在制品的缓存区。对于物料及在制品存储的管理要求是对线旁库的入库、出库操作进行记录,并按物料类别统计准确的实时库存。
7.5.3 物流调度
芯片式传感器的可重入生产工艺特征增加了物流调度的复杂性。
物流调度应以提高物料搬运效率、缩短加工等待时间为优化目标,进而提高生产效率。应基于生产工艺及物流布局,针对不同的物流调度问题采取有效的动态调度策略进行分析优化,包括物流设备、人员等资源调度和物流路径的规划。
7.5.4 物流跟踪
物流跟踪是对物料进行可追溯性管理,主要体现为对在制品的物流跟踪,主要的跟踪信息包括:在制品当前的加工/检测工序、加工/检测设备、搬运设备、物理位置、存储地点等,以及基于上述信息形成的实际加工路线。物流跟踪数据一方面为物流调度提供分析决策依据,另一方面为生产过程回溯提供分析依据。
物流跟踪的重要前提是实现对物料及在制品的身份标识和识别感知。标识编码应按照编码规则生成,通常包括批次 ID、晶圆 ID 及批计划 ID 等。
7.5.5 消耗成本统计
消耗成本统计主要包括物料消耗统计和生产产量统计两个方面。
—— 物料消耗统计:按照物料的不同类型进行分类统计,如原料晶圆的消耗和光刻胶等辅料的 消耗。消耗统计应区分正常生产消耗和质量问题导致的消耗。
—— 生产产量统计:包括成品产量以及各工序半成品产量的统计。
基于物料消耗和产量的统计,能够有效分析投入产出比,为生产成本的评估提供可靠依据。
7.6 车间设备管理
7.6.1 总则
数字化车间设备管理主要功能包括设备状态监控、设备维修维护及设备效率分析。各功能之间及与外部功能子系统之间的数据关系描述如图 9 所示。
图 9 车间设备管理功能模型
7.6.2 设备状态监控
7.6.2.1 设备运行数据采集
对于芯片式传感器的芯片生产设备,应基于 SECS 标准协议进行数据采集。对于传感器装配设备,应按照相应的通信接口进行数据采集,如以太网接口等。对于其他没有标准通信接口的设备,则需通过增加专用采集板卡或终端进行采集。对于具有设备运行日志的设备,需要能够通过网络接口实时获取日志文件,并对运行日志的内容进行解析。
数据采集信息一般包括:
—— 设备当前状态信息;
—— 设备状态起始时间信息;
—— 设备运行及空闲时间;
—— 设备故障信息;
—— 设备报警信息;
—— 设备运行参数信息;
—— 设备加工数量;
—— 合格品及不合格品数量。
7.6.2.2 设备状态展示
设备状态信息应提供图形化展示界面,以满足可视化监控要求。
7.6.2.3 异常报警
依据设备运行标准和要求,对关键运行指标和参数的监测结果进行分析和判定,对指标异常情况进行报警,并将报警信息及时通知到相应的设备监控人员,以得到及时处理。
7.6.3 设备维修维护
7.6.3.1 工单管理
应建立工单管理机制,形成以计划制订、工单分配、下发、执行、反馈为流程的标准化维修维护体系。充分利用智能移动终端(如手持 PDA、智能手机、平板电脑等)完成工单的执行和反馈。
7.6.3.2 维修维护
根据设备类型的不同按周期制订维修维护计划,基于配置信息自动生成维修维护工单,并下发给相应岗位人员,通过执行工单的反馈信息跟踪执行状态。
7.6.3.3 故障管理
a)故障分类
依据各类设备的软硬件故障类型,建立完整的设备故障分类结构。
b)故障分析与处理
采集设备故障数据,记录故障分析原因和故障处理结果,形成完整的设备故障处理档案。
7.6.4 设备效率分析
基于设备运行与维护过程中采集的数据,能够统计分析设备效率,主要指标通常包括设备完好率、设备故障率、停机时间、停机次数、设备平均故障间隔时间(MTBF)、设备综合效率(OEE)等。
7.7 车间工装管理
7.7.1 总则
车间工装管理主要功能包括划片刀管理、探针卡管理、光刻版管理等。各功能之间及与外部功能子系统之间的数据关系描述如图 10 所示。
7.7.2 工装共性管理
共性管理主要对工装的使用信息进行记录跟踪,以及对工装的寿命进行监控。
7.7.2.1 寿命监控
监控工装的使用次数,在接近使用寿命时,提醒维修人员及时保养或更换。
图 10 车间工装管理功能模型
7.7.2.2 使用日志
记录工装的使用情况和使用次数。
7.7.3 工装特性管理
特性管理主要针对工装本身的特点和使用特点进行管理。
7.7.3.1 划片刀设备绑定
对划片刀与理解设备的绑定关系进行管理,主要包括安装时间、划片刀供应商编号、供应商名称等信息。
7.7.3.2 探针卡标识管理
标识管理记录探针卡的供应商信息、供应商批号、探针使用寿命、探针类型,以及分配本系统标识等信息。
7.7.3.3 光刻版标识管理
标识管理记录每块光刻版的供应商信息、供应商编号、报废条件、使用说明、本系统标识和光刻形状说明等。
7.7.3.4 光刻版存储管理
记录光刻版的存储位置、光刻版标识、存储时长等信息。根据光刻版标识可以快速定位查找到所在位置信息。
7.8 环境监测管理
7.8.1 温湿度监测
7.8.1.1 工区温湿度监测
周期性采集每个工区的温湿度,当出现异常时,产生报警事件并进行报警处理。
7.8.1.2 工区温湿度日志
周期性记录工区温湿度情况。通过日志,可以获取任意工区、任意时间的温湿度信息,当生产质量出现问题时,可以查看当时的温湿度情况,辅助分析。
7.8.2 洁净度监测
7.8.2.1 洁净度等级配置
对工区洁净度进行分级管理,并按工艺要求,对每个工区进行洁净度等级配置。
7.8.2.2 洁净度记录分析
周期性采集每个工区的洁净度,并针对工区的洁净度历史记录数据进行统计分析。
8 系统集成要求
8.1 设备集成与控制
芯片式传感器数字化车间一般要求管控系统与主要生产设备、检测设备、监控系统进行集成与控制,应具有数据采集与指令下达双向通信能力。需要集成与控制的生产设备一般包括 PECVD、光刻机、涂胶机、显影机、封管真空机组、蒸发台、减薄机、粘片机、合金炉、划片解理机、晶片扩张机、清洗台等;检测设备一般包括显微镜、台阶仪、椭偏仪、雪崩特性测试台、半导体管特性图示仪等;监控系统一般包括视频监控、按灯系统等。
有关典型工艺设备的数据采集内容可参见附录 B。
8.2 系统集成
芯片式传感器数字化车间管控系统应具有和上层管理系统集成的能力,管控系统起到集线器的作用,相当于一个通信工具为其他应用系统提供生产现场的实时数据。例如,ERP 系统一般需要管控系统提供的成本、制造周期和预计产出时间等实时生产数据。另一方面,管控系统也要从其他管理系统中获取相关的数据,以保证其自身的正常运行。例如,管控系统中进行生产调度的数据来自 ERP 系统的计划数据。
8.3 数据存储要求
芯片式传感器数字化车间管控系统与设备、上层系统集成的数据,应根据应用要求不同存储在关系、实时历史等数据库中,且关系数据库中应根据数据集成频率、数据量大小制定合理的数据备份与数据转存机制,保证满足管控系统应用功能模块对数据的访问效率及数据安全等要求;对于与设备集成的数据,由于数据采集频率高、数据量大,因此一般将此类数据压缩存储在实时历史数据库中。